There can be 3 types of communication:
- Leadership dictates
- Conversation within a department
- Conversation between departments (e.g., operations and maintenance)
Communication breakdown occurs when there is a lack of trust between the working level and management. Similarly, the CMMS can have KPIs that present the wrong emphasis. An example of this would be KPIs that only focus on worker productivity and nothing on asset performance. It helps to remember that the CMMS is best used as an asset management system and not a people tracking system.
The Iceberg Principle
For many organizations, problems don’t always get relayed to the top. The reasons could be numerous. The figure below shows the percentage of issues that are known – but not reported. With percentages this high it is important for leadership to find multiple ways to communicate.
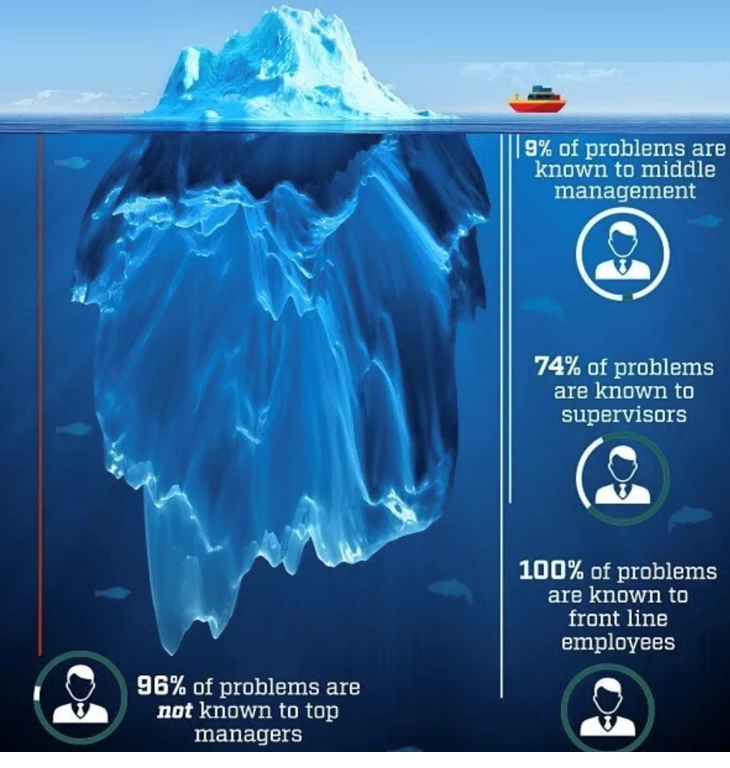
Reasons why problems do not get communicated:
- Operators marked up check-cards (paper) and turned these in, but no one had the time to convert digitally into the CMMS.
- The technician communicated this issue verbally but the supervisor forgot.
- The technician typed on the work order “This asset failed because of improper PM strategy”, but no one read the comment and acted on it.
- The operator decided not to report the problem because previous complaints went unheard.
- The asset had a design flaw but the operator assumed that nothing could be done.
- The O&M procedure was incorrect but staff knew cper word of mouth] not to follow that step.
- The operator encountered a functional failure but did not know it was a functional failure.
There are multiple ways to address the poor communication:
Training – This is a good place to start. Example training curriculums include precision maintenance skills, asset management principles & practices, CMMS navigation, advanced processes, and explaining why accurate data is needed (i.e., for accurate reporting).
Business analyst – This role in particular helps discover problems with staff, problems with data, and problems with software. The business analyst can run error checks which find hidden failures in the database.
Gatekeeper – This role prevents data errors from being carried forward under a work order.
Work order feedback – This capability, if implemented, captures technician feedback such as issues with maintainability, design, PM methods/frequency, ergonomics, and unexpected hazards.
Defect elimination teams – Defect elimination teams discover issues before they become worse.
Kaizen events – A kaizen event is something an operations shift might perform to capture ideas and document anomalies.
ODR – Operator driven reliability encourages the shift of asset ownership to the ops staff; plus, it suggests operator be trained to perform minor maintenance.
Chronic failure analysis – CFA involves a bad actor report which drills down on failure mode to cause.
Root cause analysis – RCA is a significant event which assesses the root cause to prevent recurrence.
Asset criticality – By applying a risk-based criticality to assets, the asset management stakeholders can focus on the right assets with the right strategies at the right time.
RCM analysis – This analysis helps determine the likely failure modes which in turn enables staff to identify the best maintenance strategy. By documenting these failure modes, O&M staff knows what to look for.
Posters/collages – Posters and collages enhance communication. A properly illustrated story stays with the reader and helps explain complex processes.
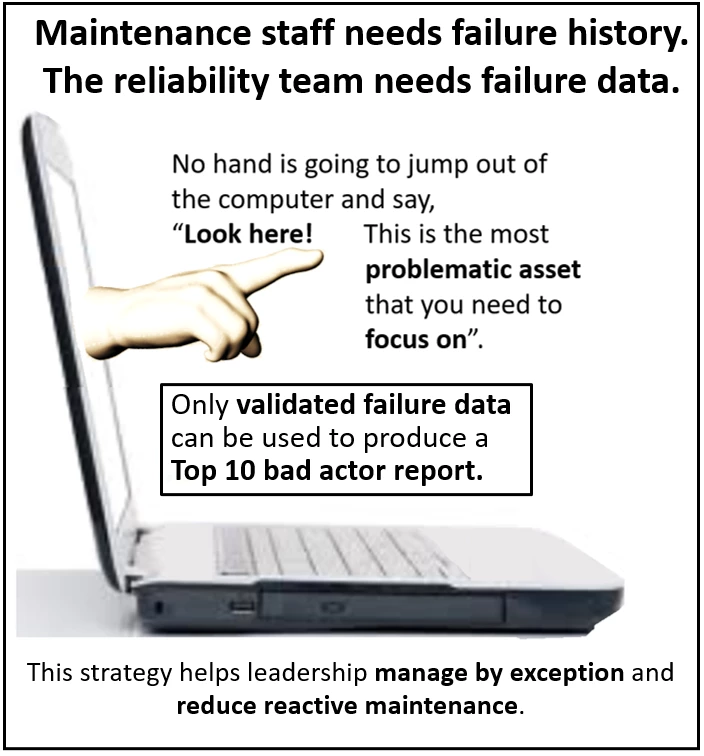
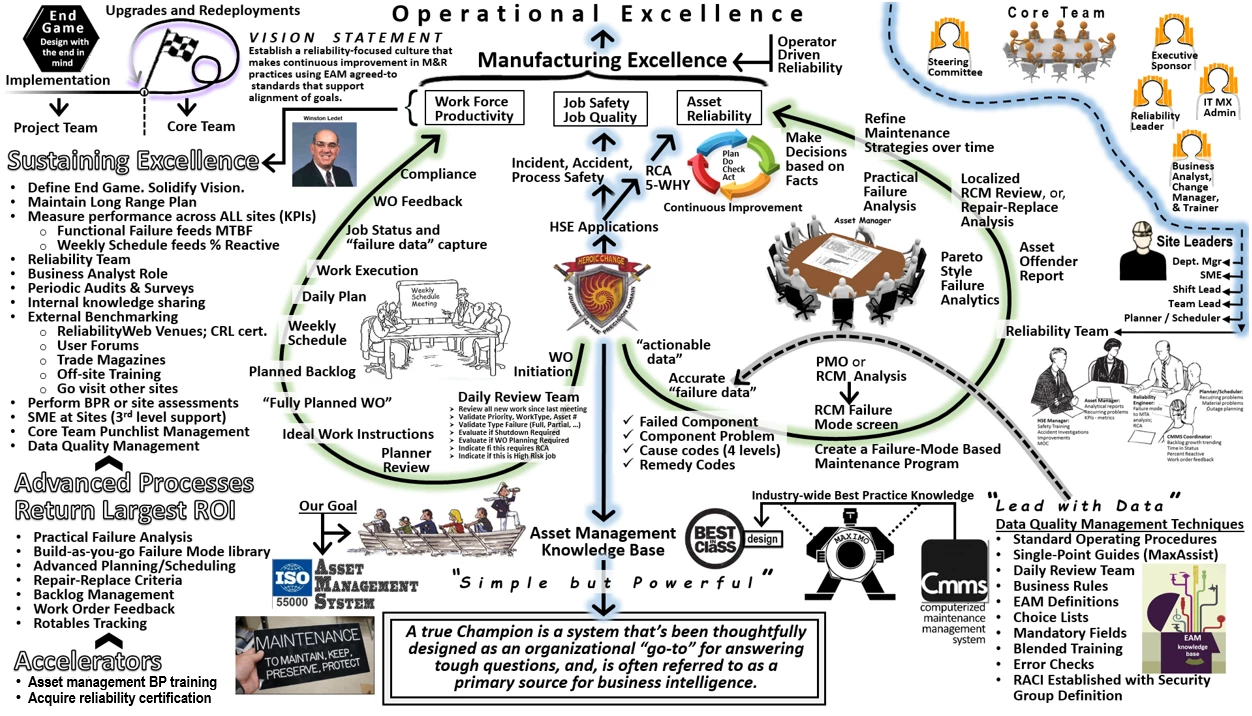
The Importance of Operator Driven Reliability (ODR)
Operators are encouraged to perform minor maintenance so that maintenance technicians can focus on complex jobs and backlog reduction. ODR requires operations personnel to recognize anomalies and failure modes. Properly trained operators can better assess and manage the reliability aspects of assets and systems.
The impact of most equipment failures can be minimized when operators “know” their equipment and understand what “normal” and “abnormal” looks like.
The goal is to minimize repair costs, reduce down time, mitigate or eliminate safety hazards, and even extend equipment life. But ultimately, an operator’s goal is to improve the plant’s output in terms of quality, efficiency and safety, while complying with applicable regulatory requirements. The unreliability of equipment coupled with a failure to detect problems in advance can cause catastrophic events.
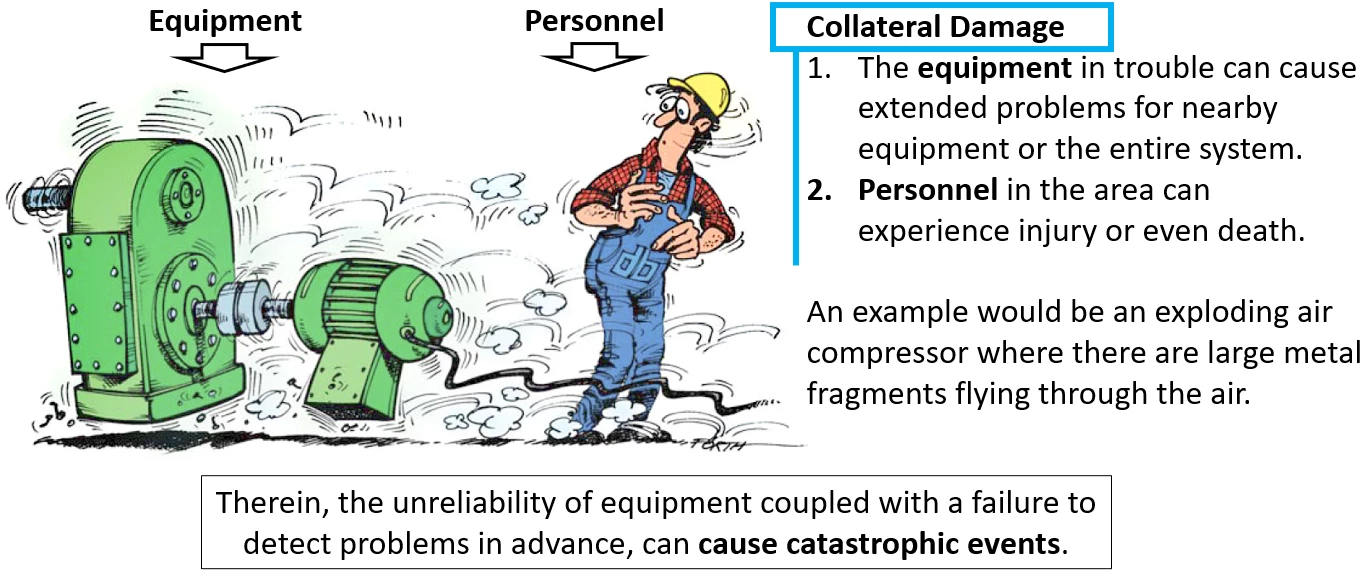
Check-Cards Help Improve Communication
When operators operate equipment, they observe anomalies. The question becomes, do they communicate these issues to the next shift, and more, importantly to the maintenance staff? Lastly, who receives these checks cards and does the information get entered into the CMMS as work orders?
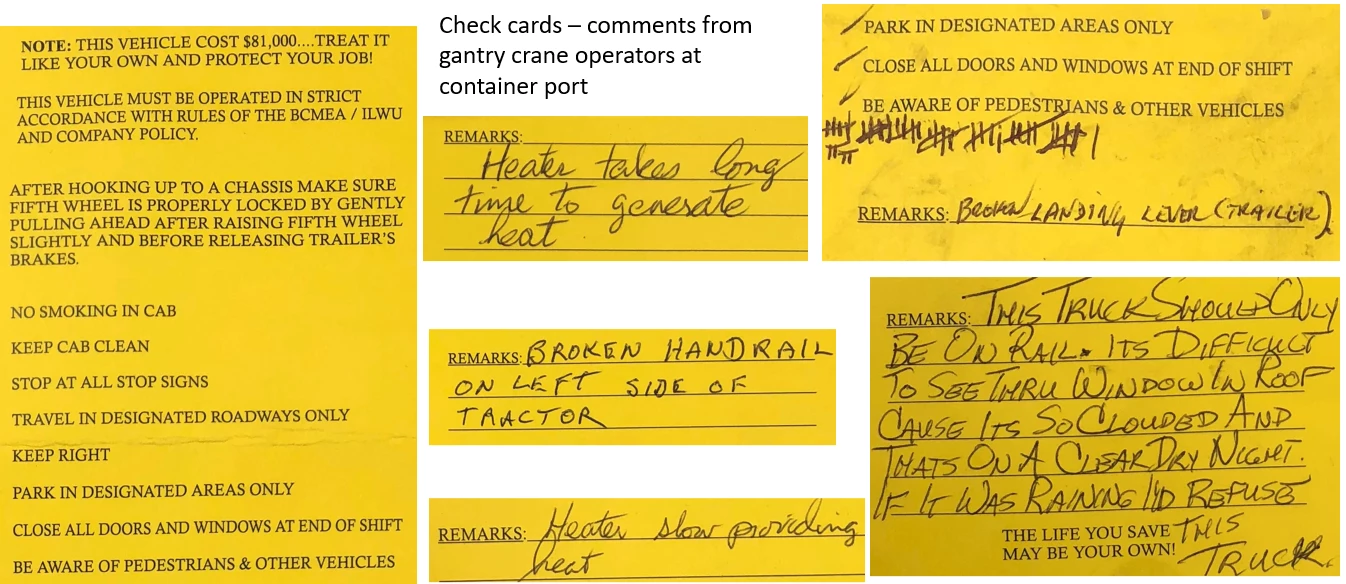
Kaizen Teams Support Better Communication within the Department
In business, kaizen refers to any activities that improve the function of a process. Kaizen in the workplace can boost efficiency and productivity. At the end of each shift, operations staff may set aside time to share ideas for improvement and of course, problems. There may be a kaizen board (shown below) which shows metrics, status, and on-going problems. A facilitator may lead the session.
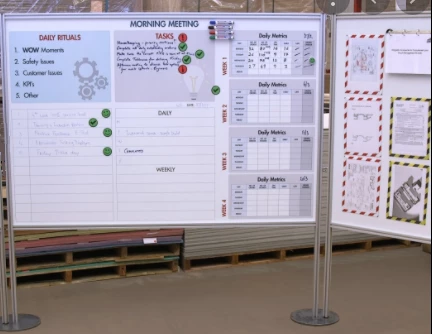
Do you use any of these tactics at your organization to avoid poor communication? Are there any others you’d like to highlight here?