Some organizations form defect elimination teams which include representatives from operations, maintenance, and engineering. This team may be assigned to performing a walk-down of a problematic system. When issues are discovered, they may be tagged and assigned a work order, but in some cases, the defect team may perform an immediate fix. As shown in the figure below, defects can be introduced anywhere in the life cycle.
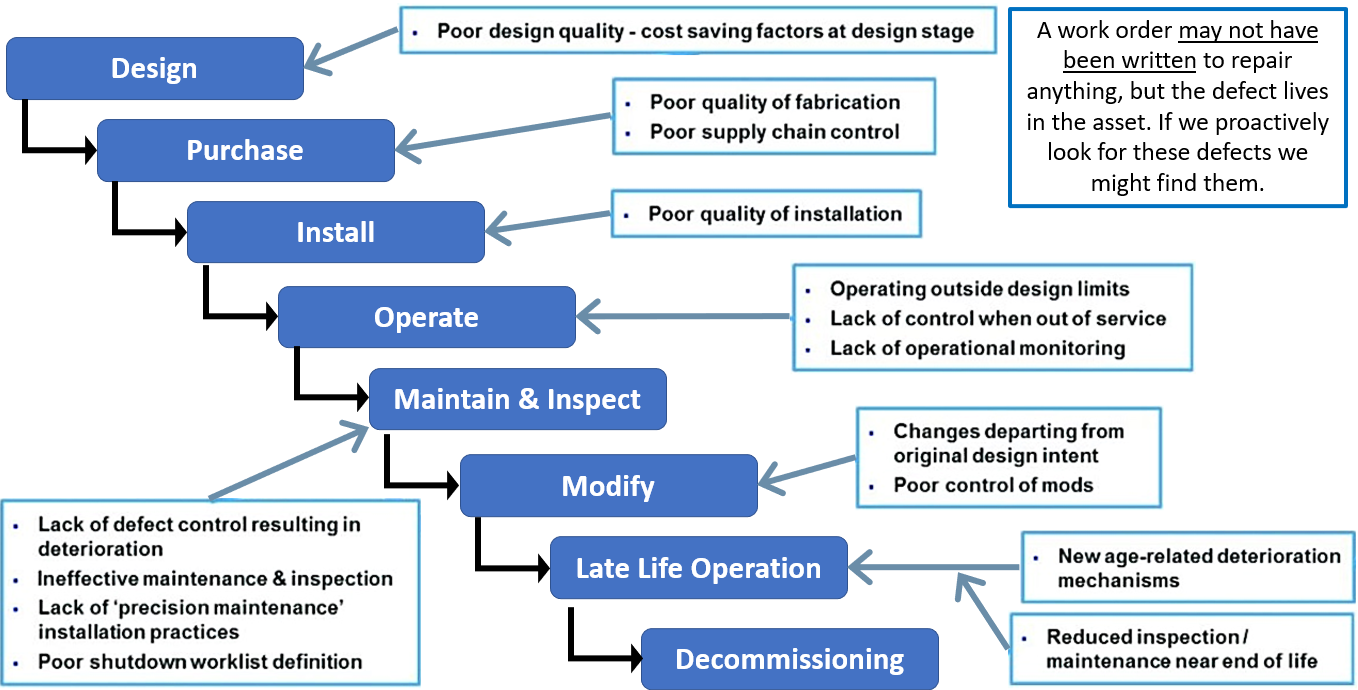
Example Defects
- Operating procedure incorrect
- Excessive rust/corrosion
- Broken indicator light
- Potential hazards; missing guard covers
- Excessive fluid leakage; oil leakage at joints
- Pipe hangers missing (or not adding proper support)
- Defective wiring; broken conduit; broken junction box
- Operating valves not tagged (as commonly used in LOTO)
- Sight glass broken; Gage missing acceptable range coloring
- Gage too small -- ergonomic issue; proximity sensors not working
- Missing CMMS Asset Identifier; Asset altogether missing in CMMS
- Housekeeping (cleaning) needed – which may display other problems
- Engineering issue (design flaw); alterations made but not recorded in drawings
- Belts being replaced at too frequent an interval due to some unknown problem
Does your organization have a defect elimination team?
If so, tell me about it in the replies