We’ll get straight to the point: Managing parts inventory is a pain in the a$$.
Between just-in-time, rolling average, or sawtooth, there’s no perfect method to accurately predict what parts you’ll need on hand. It generally requires hiring an inventory manager, studying models like economic quantity order (EOQ) and lots of spreadsheets.
But there’s a better way.
Fiix just launched its parts forecaster, which automatically sorts through a bunch of data in your CMMSÂ and helps you find trends so you can keep the right parts on hand.
Â
What is the parts forecaster and how is it different?
Â
The parts forecaster works with the parts feature in your CMMS. Instead of relying on spreadsheets or complicated inventory models, it uses your real historical data to predict parts use and make inventory recommendations.
It’s the first feature built on our Fiix Foresight AI engine. Since it runs on AI, the parts forecaster can look at a lot of data really quickly. And it’s built right into your CMMS, so it takes things like upcoming scheduled maintenance, predicted reactive maintenance, and your current inventory stock into account when making purchasing recommendations.
The forecaster even accounts for factors like seasonality and can quickly adapt to any changes you make to your maintenance program to keep recommendations accurate.
The best part is, these recommendations are delivered to your inbox in a simple report whenever you want it (daily, weekly, or monthly). That’s it— no cost, no coding, just more accurate parts forecasting.
Â
How does it perform in comparison to traditional forecasting methods?
Â
Here’s a burning question that all our customers have: When it comes to traditional forecasting methods, how does the parts forecaster perform?
Sawtooth or min/max
In the sawtooth method, purchase orders are made based on current inventory levels. When stock reaches a reorder point, the inventory manager orders a specific quantity to ensure stock will never dip past the minimum. This method is ideal for minimizing the risk of stockout. However, having a safety stock on hand encourages inventory managers to carry a large inventory, which ties up working capital.
With the parts forecaster, purchasing recommendations take predicted parts usage into account. We make sure you have exactly what you need, and at the right time, so you don’t have to keep a large safety stock to avoid stockouts.
Just-in-time
We typically see the just-in-time method in lean manufacturing, where inventory managers order parts just before they’re needed. This lets them reduce inventory and minimize working capital, but it’s tricky to keep the right balance. Without a safety stock in place, teams that use just-in-time are often prone to stockouts.
The parts forecaster helps by automatically analyzing all historical parts and maintenance data in the CMMS to accurately predict upcoming parts usage to avoid the risk of stockouts.
Rolling average
In a rolling average approach, inventory managers look at average parts consumption over 2-3 weeks to inform purchasing decisions, and order parts on a fixed and recurring schedule. While this is arguably an easier method to adopt, it can be highly inaccurate. For example, changes in demand based on seasonality can cause stockouts or result in overordering of parts.
The parts forecaster can spot patterns in your maintenance practices, like seasonal trends. It will leverage these insights to give you accurate parts predictions and purchasing recommendations.
Early beta customers using the parts forecaster are seeing a 50% increase in parts forecasting accuracy and up to 40% reduction in stockouts. Additionally, customers that follow the report recommendations have seen a 50% reduction in working capital reserved for parts.
Â
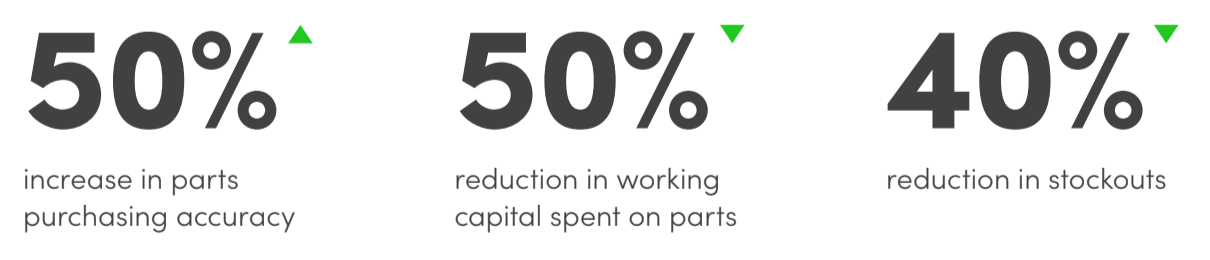
Â
And that’s just the tip of the iceberg. The magic of artificial intelligence is that the more these models are used, the more accurate they become, so as more customers start to take advantage of the parts predictor, you’ll see those numbers start to improve considerably.
Â
How do I take advantage of it?
Â
The parts forecaster doesn’t have to replace your existing processes. We’ve seen our customers use the report for many purposes:
- Inform purchasing decisions: If you don’t currently have an inventory process in place, you can skip the legwork and go straight to using the parts forecaster to determine your parts reorder quantities.
- Confirm and adjust purchasing quantities: If you are already using one of the inventory models we mentioned earlier, you can always cross-reference the parts forecaster with your existing purchasing plans to identify areas for improvement. We see a lot of customers adjusting their ordering quantities based on the predictions in the report.
- Improve processes: Since the accuracy of the report is based on parts usage data, you can also use the report to pinpoint areas of improvement in your parts tracking process. Better yet, as you continue to improve your processes, your report accuracy will improve!
Â
How do I get started?
Â
Having the right parts on hand is crucial for operating an efficient maintenance team. We’ve seen so many customers struggle to keep inventory under control so we built the parts forecaster to help maintenance teams easily get accurate insights.
This is where it gets really exciting: We’ve done everything in our power to make setting up our parts forecaster super straightforward. As long as you’re a Fiix customer currently using the parts and supplies module, all you need to do is reach out to your customer success team. They will ask you a couple of questions about how you want to set up your report and our team will start running the forecaster right away.
Â