While many things in maintenance are not predictable, equipment maintenance logs are. They help you perform preventative maintenance to ensure equipment is in good condition, runs as efficiently as possible, and provide a useful reference point for discovering failure patterns, expenditure, and repair.
This post will explore how you can create and maintain a top-notch equipment maintenance log and the 6 ways you can make the most of the data you’re collecting within them.
How to create an equipment maintenance log
This will all depend on a variety of factors that are specific to your team and facility, but any log should keep these 3 questions in mind:
- What asset and maintenance information do you need most?
- How detailed does that information need to be?
- Who will be using this information and how will they use it?
Your log will include two sections:
Asset Information | Maintenance Work Information |
|
|
You should end up with something like this:
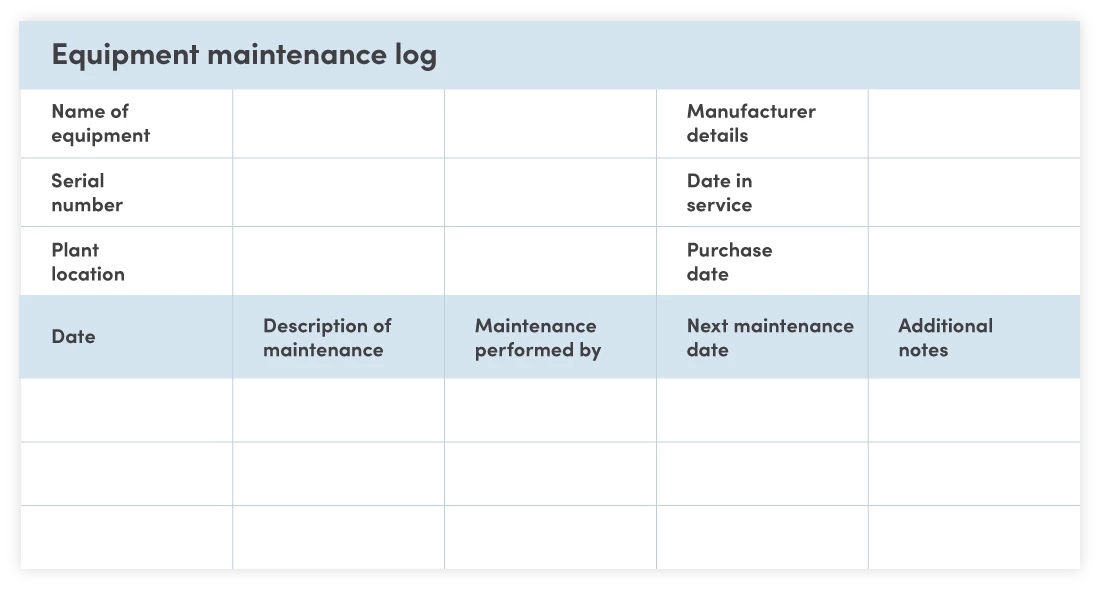
Pro tip: You don’t want to make it hard for technicians to complete the log, so keep descriptions short and have all key details laid out plainly.
How to maintain your equipment maintenance log
Follow these 3 simple rules:
- Create a standard template for every asset to avoid errors and make future data analysis much easier.
- Keep your logs in a designated location so they are easy for all maintenance workers to find.
- Have a routine for exchanging logs between shift changes so everyone is kept in the loop on completed or outstanding work, problems, safety risks, and other useful information.
6 ways to use data collected in equipment maintenance logs
A well-kept equipment maintenance log can help you create a better future for your assets, maintenance team, and organization.
Maximize equipment ROI |
|
Optimize preventive maintenance schedules and tasks |
|
Track preventive maintenance compliance |
|
Identify opportunities to upgrade your maintenance strategy |
|
Improve accountability and communication |
|
Make training and onboarding easier |
|
By following these steps, your equipment maintenance logs will become the best way to use the past to create a better future for your facility and its assets.
What are your tips for making the most of your equipment maintenance logs? Share them in the thread below.