When it comes to work order planning, no one wants to constantly take two steps forward and one step back. In this post we’ll explore the best practices and simple frameworks for strong maintenance planning and work order scheduling.
Â
Planning
There are two ingredients you need to be really good at planning work orders:
- Clear goals for maintenance that align with the goals of the organization
- A way to prioritize maintenance activities based on your goals
All of your work processes, schedules, training, and SOPs flow from your goals and priorities.
“You really need to go back to the fundamentals of the organization and find out what their objectives are for maintenance,” says Charles Rogers, a Senior Implementation Consultant at Fiix with over 33 years of experience in maintenance and reliability.
Â
Four steps for aligning maintenance goals with business goals đź§
Follow this 4-step process to align your organization’s goals with your maintenance plans:
- Confirm the goals of your organization. This could be something really specific, like decreasing the cost-per-item, or something a little less tangible, like entering new markets.
- Link maintenance KPIs to business goals. If reducing the cost-per-item is the big goal, maintenance could focus on reducing downtime and maintenance costs. If entering new markets is the target, you might want to standardize maintenance processes so they can be repeated at other sites.
- Choose your maintenance metrics. Set up metrics and benchmarks so you can track progress and measure success. For example, if you want to prevent unplanned downtime, you might track faults found and fixed through PMs on critical equipment.
- Plan maintenance activities to hit your targets. Let’s say your aim is to find problems with critical equipment before they cause failure. In this scenario, you have to figure out what your critical equipment is, how often it should be inspected, and what needs to be included in work orders for those assets.
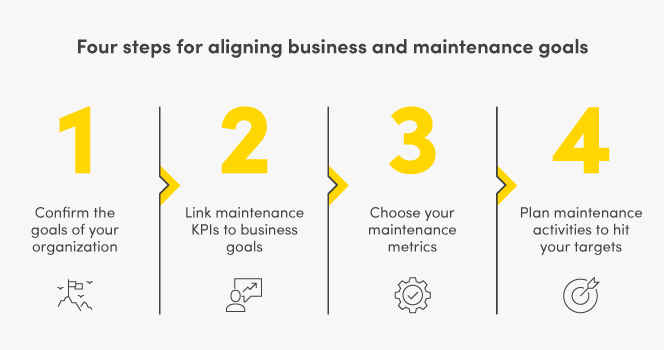
Scheduling
The number of failed inspections per PM is the true mark of scheduled maintenance success, says Charles. Every problem you catch during a PM is an asset failure avoided.
And that’s the secret to really good maintenance scheduling: The constant tweaking of PM frequencies to find the right balance between too often and not often enough.
Â
How to optimize preventive maintenance frequencies 
Use the PDCA model (Plan, Do, Check, Act) to help you find the right PM schedule over time:
- Plan:Â Create a baseline for PM frequencies by looking at recommended guidelines, repair history, criticality, and usage patterns for an asset.
- Do: Follow your plan consistently for accurate results.
- Check:Â Look at failure metrics for each asset to determine if your plan is working.
- Act: Fine-tune your PM frequencies based on your findings. Increase the frequency if an asset is breaking down between PMs. Reduce the frequency if your PMs don’t find failures or if the number of breakdowns between PMs is low.
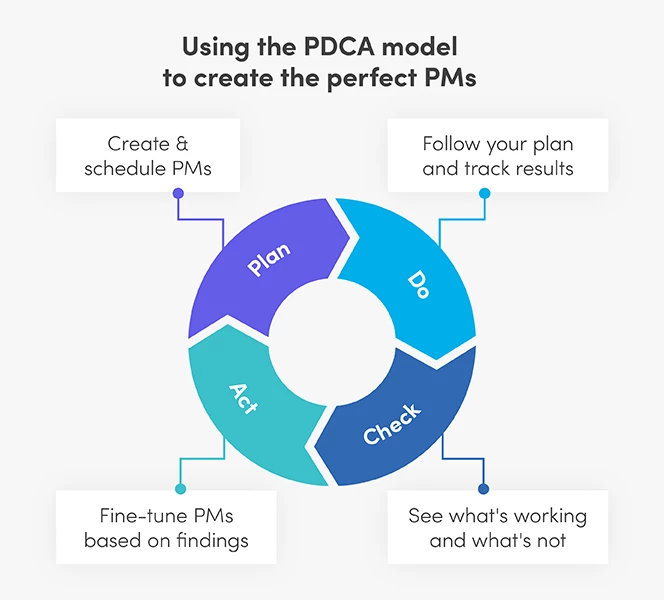
Warning: This process is not quick. It takes a while to go around this cycle and implement improvements. But you will see improvements, including longer MTBF intervals, fewer labor hours, and fewer costs for spare parts and supplies.
Â
Remember to schedule around seasonality and sudden production changes 
In a perfect world, plans would never change and your maintenance schedule would run like clockwork. But we don’t live in a perfect world. The holiday season can lead to a huge spike in orders.Â
When things shift at your company, your maintenance must shift too. One way to stay flexible is with your maintenance schedule. This doesn’t mean abandoning all the plans you’ve put in place. Actually, it’s the opposite, says Charles.
“This is when it’s super critical to understand your asset criticality and asset priorities,” says Charles.
Knowing the needs of each critical asset is what helps you create schedules and justify the maintenance windows required to ensure healthy equipment.
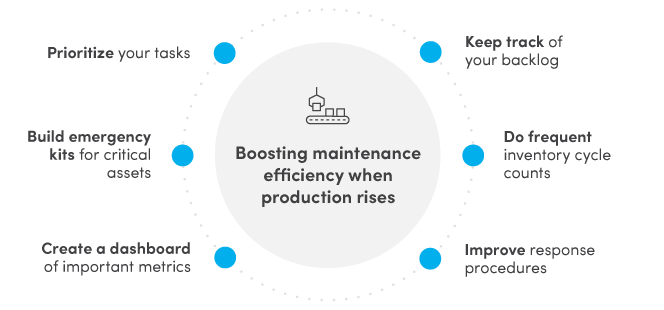
“It also becomes very critical to understand how assets need to be shut down and started back up so that they function as best they can in those situations,” explains Charles.
Plan work orders that cover all the nuances of each equipment and each task. Build airtight SOPs with this information so delays don’t make stopping and starting equipment even harder.
Here’s everything you just read in three sentences:
- Having crystal clear goals for your work orders will give you a clear direction for all your decisions around maintenance planning and scheduling.
- Never set your maintenance schedules in stone and always keep looking for ways to optimize each work order so you’re doing it at the right frequencies.
- Your work order plans and schedule won’t always be popular with everyone, but having proof that they work will help you justify your strategy and allow you to follow through with it.