While many projects can take months or years to complete, getting quick wins is crucial for building momentum and proving value for your maintenance team.
In this article, you’ll learn five processes that your maintenance team can put in place quickly to help increase production efficiency.
1. Optimize the frequency of your PMs
Going overboard on preventive maintenance can affect production efficiency in a few ways. It can either waste valuable time preventing non-existent failure or increase your risk of failure by meddling with a perfectly fine component.
There are a few guidelines to consider when trying to find the right balance between too many and too few PMs:
- Use equipment maintenance logs to track the found failure rate on preventive maintenance tasks (Tip: start with PMs that take the longest to do or cost the most)Â
- If a PM leads to regular corrective maintenance, keep it at the same frequency
- If a PM rarely identifies failure, try increasing the time between inspections
- If the found failure rate exceeds the frequency of the PM, tweak your schedule so it’s better aligned
- If a machine experiences frequent breakdowns between inspections, try shortening maintenance intervals.
- You can also modify the trigger for maintenance and change it from a time-based trigger to a usage or performance-based trigger
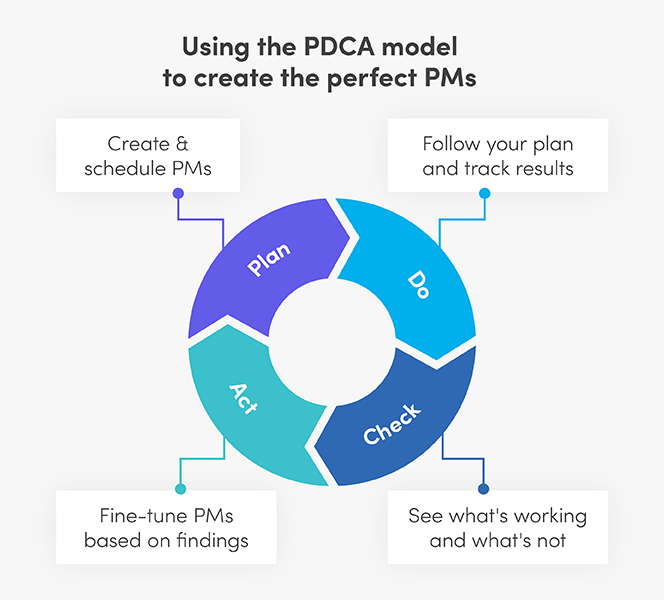
2. Identify machines that can be maintained while running
Some routine maintenance can be done while a machine is still operating. Find out if any assets can be safely worked on while being used for production.Â
This might mean that some work can’t be done because certain areas of a machine aren’t safely accessible while in operation. In those cases, determine if partial maintenance is possible and if it’ll positively impact the equipment’s performance.
It’s also good to track rotating or spare assets and swap them for production equipment when possible, as that will allow you to do regular maintenance on those machines without sacrificing productivity.
3. Make equipment capabilities transparent and clear
Create an iron-clad list of instructions for operating equipment and common issues to be aware of. You can use a failure modes and effects analysis (FMEA) to create a list of common failures experienced by each asset. This can also include warning signs for breakdowns.
Having this information clearly outlined and easily accessible gives operators a chance to notice the early signs of failure and notify maintenance before it gets worse. Employees will be empowered to observe and identify any potential problems (and report them accordingly).
4. Use work order data to identify where your team can be more efficient
Work order data can tell you what jobs can get done quicker and how to minimize the risk of asset failure so you can boost production efficiency.
Here are a few telltale signs of broken processes in your work orders:
- Unavailable parts and supplies: if this issue could delay maintenance, review the purchasing process for parts and supplies. That includes ensuring your cycle counts are accurate and the threshold for purchase approvals is low enough that inventory can be replenished quickly.Â
- You can also create parts kits for frequent repairs or emergency repairs on production equipment so your team can locate and retrieve parts quickly.
- Misidentified/misdiagnosed problems or missing instructions: Make sure task lists, failure codes, and descriptions are clear. Attach photos, manuals, and other documentation to the work order.
- Diverted resources resulting from emergency work orders: Analyze your work order data, find tasks that are too big, and break it down into smaller jobs to reduce the risk of major disruptions.
- Scheduling conflicts with production: See if maintenance can be scheduled during production or if work can be done at alternate times like evenings or weekends. You can also consider giving operators minor maintenance responsibilities associated with the work order.
- Lack of adequate worker skillset: Make it clear on work requests what skills or certifications are necessary for certain maintenance types.
5. Find the biggest obstacles for your team and eliminate them
You can learn a lot from data that comes from your equipment and work orders. But sometimes, you just have to ask the people doing the actual work as they can only tell you what barriers they face when completing it. Acting on this information is extremely important as you look to improve your maintenance processes, as all those improvements can lead to a huge boost in production efficiency.
For example, your technicians may spend a lot of time going back and forth from the office to retrieve manuals, asset histories, or other materials that help them on the job. You probably won’t know that just by looking at work order records or wrench time reports. Armed with this information, you can figure out a solution. You may end up creating areas throughout your facility where files can be accessed for nearby assets or end up digitizing those files so they can be accessed through a mobile device.
To do this, consider asking these questions to your technicians:
- What tasks commonly take you away from a machine?
- Are information and parts easily accessible? If not, why?
- What information would help you complete work more efficiently?
- Are there processes or systems that are hard to use or you think could be improved?
- Is there anything that frequently keeps you from starting a task on time?
What does your facility team implement to keep your production efficient? Let us know in the comments below.Â