Check out how the world’s biggest toy manufacturer gamified maintenance with AI to beat downtime and reduce the cost of production in our latest case study. This is a holiday edition case study. All facts, figures, names, and allusions to imaginary corporations run by a man in a red suit are fictional. However, the benefits of using Fiix and the latest product features are 100% real.
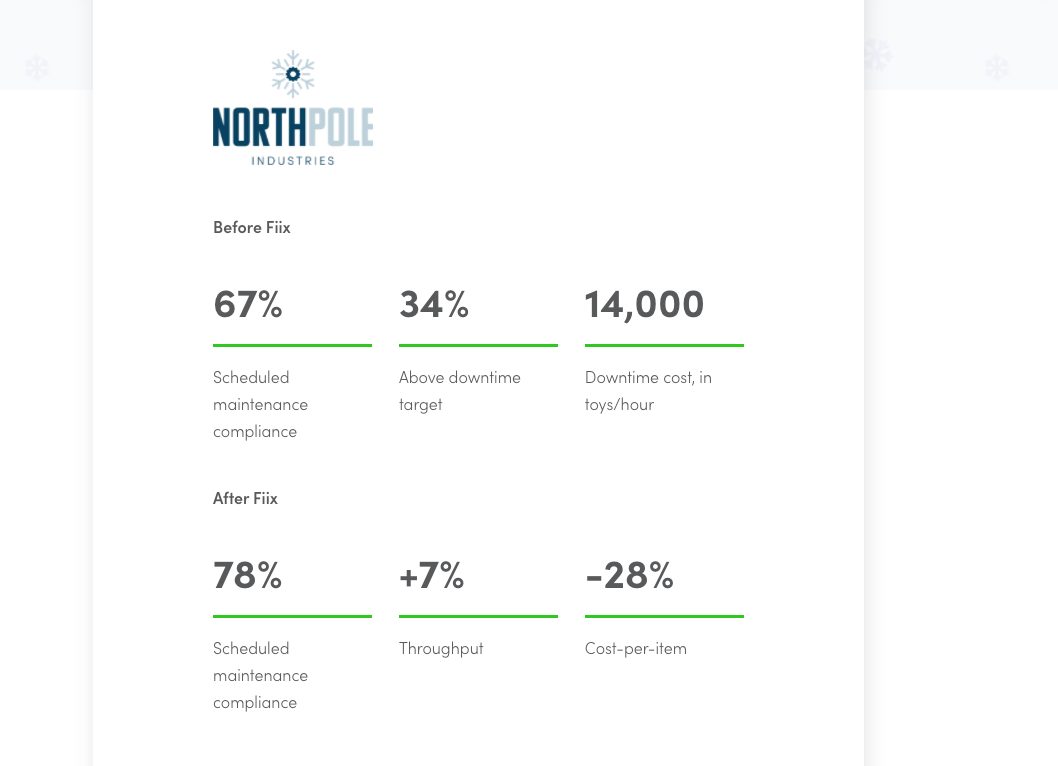
The company had to make more than 22 million toys in under four months. With so many different products on order—phones, baseballs, Lego sets, etc.—there was little margin for error.
“Breakdowns happen, that’s just a fact of life in manufacturing,” says Yule Elfson, NPI’s Manager of Operations.
“But we can’t afford less than 98% availability during the busy season. That’s why we value scheduled maintenance so much. We know it’s coming. We can plan for it. It keeps equipment running.”
Listen to Yule Elfson describe what it felt like when three lines went down at the same time -->
“Doing reactive maintenance can be addictive,” says Claus.
“You fix a machine and people would literally cheer for you. It’s like being a superhero. It feels good in the moment, but it means our preventive maintenance is slipping, which was leading to more downtime.”
“People used to stop technicians in the hall to give them work,” says Claus. “Now they’re stopping them to say thank you for the impact they’re having. That sort of recognition was way overdue and has raised the morale of the team more than I can measure.”
“It’s something we’ve been wanting to do since we switched from reindeer to autonomous delivery vehicles. We can cut down on maintenance resources we don’t need to spend while shrinking our carbon footprint.”
The team had so much fun with this one! Please check it out and we hope you enjoy reading it as much as we enjoyed putting it together.
Happy Holidays