In recent years manufacturers and by extension, maintenance teams, have faced a series of challenges from pandemics, supply chain slowdowns, and now a demand for skills in the workforce that are difficult to come by. At the same time Industry 4.0 technologies—such as automation, IoT, AI, and advanced robotics have streamlined many production processes, and the demand for skilled workers who can operate, maintain, and optimize these systems has subsequently increased.
It’s become clear that there’s a widening gap in skills for manufacturers aiming to remain competitive. But without a workforce that’s knowledgeable in digital tools and systems, operational efficiency, productivity, and overall equipment effectiveness (OEE) are at risk.
In this blog we will address the current skills gap facing manufacturers and maintenance teams and provide solutions to upskill the current workforce, and strategies to address skill gap challenges.
What is the skills gap and why has it become critical?
The skills gap refers to the issue surrounding current labor markets where finding workers who have the manual, operational, and technical skills necessary to work in manufacturing and by extension, maintenance has become tiresome and difficult. According to our State of Smart Manufacturing (2024) report, attracting new employees with desired skillsets has become the number one obstacle manufacturers are facing in terms of their growth. Additionally, in the previous year’s report (2023), 84% of respondents identified employee retention as their top obstacle. This data tells us that not only has the demand for skilled workers increased, so has the desire to retain these workers.
The skills gap has then slowly creeped up to becoming a big concern as of late. Some of the key reasons why are:

Rapid technological advancements: Industry 4.0 has introduced things like automation, artificial intelligence (AI), Internet of Things (IoT), and predictive maintenance (PdM). These things require a workforce that’s knowledgeable in data analytics, machine learning (ML), and machine operation. Many workers, however, lack the skills to manage and maintain these systems.

An aging workforce: A big portion of the manufacturing and by extension maintenance workforce is nearing retirement. As these skilled workers leave, there’s a shortage of younger workers to fill their roles.

Lack of necessary training and documentation: Without proper training programs and up-to-date documentation, current employees cannot effectively operate and maintain advanced systems. There’s also the challenge of little to no team members available to train new employees who are onboarding.

Declining interest in trades and technical education: There’s been a societal shift that emphasizes college and university degrees over vocational training and technical careers. As a result, fewer young people are pursuing the skills needed for manufacturing and maintenance roles.
As these challenges merge, the skills gap becomes an important factor in the disruption of daily operations. It also jeopardizes long-term competitiveness in a changing industrial landscape, and also causes a productivity decrease and safety risk.
“The challenges teams are facing today in terms of skills gap causes a lot of disruption. For one thing, there’s a decline in productivity that’s a result of limited knowledge and expertise, then there’s the inability to use any new technologies since workers aren’t trained or skilled in them,” says Jason Afara, our Director of Solutions Consultants. He adds: “There’s also safety considerations, like the improper use of machines and equipment, failure to follow safety protocols, risk of equipment failure…all of these things tie back to the skills gap.” A final point Jason highlights is that the skills gap also puts additional strain on your best team members, since the team is often going to them to do more.
With so many risks to consider, what can teams do to mitigate and manage the challenges quickly?
“Well, the good news is there’s lots of ways to manage the skills gap, and we’re in the age of AI. Teams can start using AI to track data, retain knowledge, and manage processes,” says Jason. He adds: “We already do this on our CMMS for maintenance teams and have a knowledge repository for assets so that things don’t get lost if a skilled worker leaves or isn’t available.”
Jasons points present an interesting solution for manufacturers and maintenance teams to consider when addressing the skills gap. Leveraging technology like AI has grown in popularity, in fact, according to our State of Smart Manufacturing (2024) report, manufacturers believe that GenAI or casual AI is the #1 technology to address workforce challenges. Additionally, 83% of respondents anticipate using GenAI, making it the #1 on the list of technological investments for 2024.
Solutions for upskilling the current workforce
Aside from leveraging AI, there are many different solutions to upskill the current workforce, one of the most obvious is for organizations to invest in training and development. This can take many different forms but the best steps to follow are:
- Emphasizing the importance of continuous education and training for existing employees by having mandatory course credit requirements per year.
- Investing in training programs like on-the-job training, online courses, and certifications.
- Incentivizing managers and people leaders to foster a culture of education and upskilling. This can take the form of financial incentives (i.e., bonuses).
- Tip for teams having trouble finding time to train their staff: You likely can’t take the entire team off the floor, but you could set aside some time to train team members once a week to ensure there is proper coverage on the floor.
Additionally, there’s also leveraging technology for upskilling. Employers can have their teams use e-learning platforms and virtual reality (VR) for practical training. There are even companies that offer VR training and specific authorized training centers, which is something companies can utilize to be most cost effective. Organization can also partner with educational institutions, this can include:
- Partnering with local colleges, universities and trade schools to create tailored training programs.
- Developing apprenticeship and co-op programs as pathways to development.
We recognize the importance of partnering with educational institutions to lessen the skills gap. So, we’ve developed a relationship with different educational institutions to continue the growth of a healthy talent pool for ourselves and our partners.
Using technology and automation to address the skills gap
Beyond just educational solutions, teams can also use automation and technology to help narrow the gap in the workforce. But integrating automation is a supplement, not a replacement for skilled workers. That being said, automation can bridge the gap over time by taking on routine tasks that don’t require a high-level of experience or expertise.
As Jason explains, “automation can cut the pressure on the business and teams who are lacking skilled workers… for example, technicians can use technology like a CMMS or specialized machine operations to help with automated and human tasks.” Let’s clarify what’s automated versus human tasks with some examples:
- Automated tasks: Routine inspections, data collection, inventory management, and certain aspects of production processes like welding or assembly can be fully automated. These processes can be performed with greater speed and accuracy by machines, reducing the need for a large workforce in these roles.
- Human-centric tasks: On the other hand, tasks that require critical thinking, creativity, and decision-making, such as diagnosing machine malfunctions, developing new production processes, or maintaining human-machine collaboration, remain reliant on human expertise. Human workers are essential in overseeing operations, managing automated systems, and troubleshooting when machines encounter unforeseen problems.
The good news is that by leveraging automation and technology, organizations can optimize their operations without sacrificing human touch. Additionally, people can work on more creative problem solving versus routine laborious tasks.
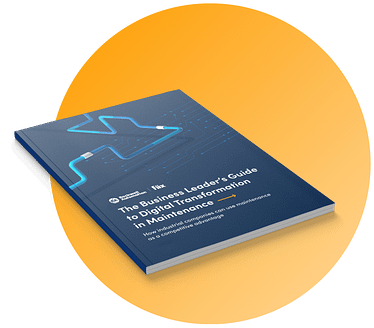
Check out our guide to digital transformation in maintenance
Human-machine collaboration and the skills gap
The role of workers will shift from performing manual tasks to managing, monitoring, and optimizing the performance of automated systems. Human-machine collaboration will allow for greater efficiency and productivity, but it requires a shift in mindset and skill set. Workers need to be equipped with the technical know-how to operate and collaborate with these advanced systems.
“To make the shift successful and less painful, companies got to invest in training and upskilling their workforce,” says Jason. According to him training should focus on three core areas:

Technical proficiency: Employees need to learn how to operate, maintain, and troubleshoot the automation tools and systems in place. This may include training in data analysis, machine learning, or how to use predictive maintenance software.

Soft skills: Workers must also develop skills in communication, teamwork, and problem-solving to collaborate effectively within a tech-enabled environment.

Succession planning: Managers should lead crossover meetings and have open communication with their employees to foster a positive culture.
Many forward-thinking companies have already embraced human-machine collaboration with impressive results. For instance, Fiat Chrysler Automobiles introduced collaborative robots—known as cobots—to work alongside their human employees on the production line. Cobots handle repetitive and physically demanding tasks, while human workers focus on quality control and problem-solving, creating a balanced workflow that leverages the strengths of both. This example demonstrates how a business can close the skills gap by embracing automation, not as a replacement for human workers but as a complement that enhances their capabilities.
Closing the skills gap will lead to more efficient operations
Addressing the skills gap in the manufacturing and maintenance sectors is crucial for the industry’s growth and resilience. By upskilling the current workforce and attracting new talent, businesses can bridge this divide and position themselves for long-term success. Industry leaders must take proactive steps in workforce development—whether through internal training, partnerships with educational institutions, or collaborations with recruitment.